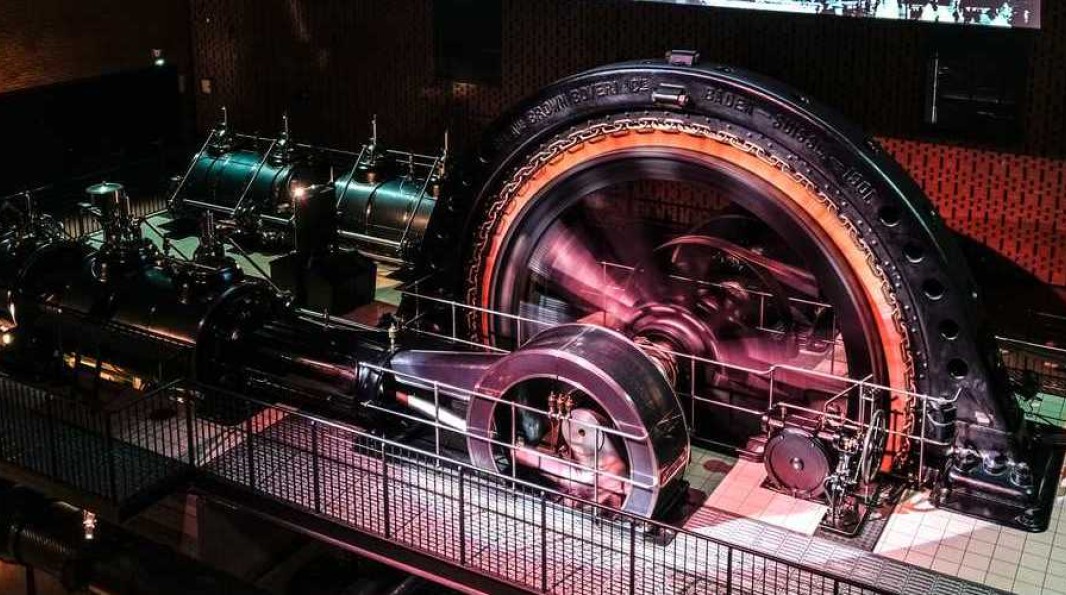
Highlight of the collection, the great Sulzer-BBC machine is at the origin of the museum's creation : it provided electrical power to the D.M.C. (Dolfus, Mieg and Co.) spinning mills of Mulhouse from 1901 to 1953.
Saved from destruction in the 80s thanks to the determination of a group of industrialists and history lovers, it was restored and transferred to the main building of the museum that was created for this purpose. What is commonly referred to as "the Great Machine" is today the pride of the industrial heritage of Mulhouse.
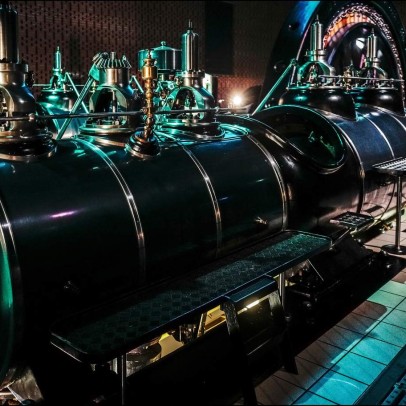
A 170-ton metal monster
This foreign-built compressor has a Brown-Boveri and Co (BBC) alternator manufactured in Mannheim, Germany. It is powered by a Sulzer steam machine, manufactured in Winthertur (Switzerland).
It perfectly illustrates the technological transition phase between steam use, the main energy source at the beginning of the industrial age, and electricity, corresponding to the second industrial period.
The furnaces produced steam at a pressure of 12 bars that operated four pistons of the steam machine contained in the four cylinders: high-pressure, medium-pressure and 2 low-pressure cylinders.
The movement of the pistons, transmitted by connecting arms and crank arms, sets off the alternator's giant wheel. The wheel also acts as a flywheel: its mass stabilizes the machine's movement... It provides alternative current by way of its 72 electromagnets, which were powered by direct current from a direct current generator called an exciter. The poles of the electromagnets are alternated: one north, one south...
When the wheel, which is the alternator's rotor, turns, the rapid changes of the magnetic field in front of the fixed component - the stator - generate an alternative current in its copper armatures. The alternator then produced a 900 KW electrical current with a voltage of 400 V and a frequency of 45, then 50Hz as of 1922.
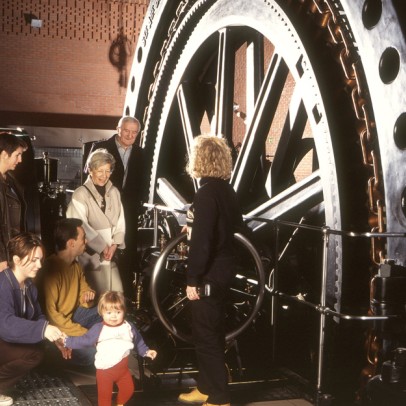
A machine among men
Trained personnel ensured the machine's proper functioning. As of 4 am, the boiler operators supplied coal so that the required pressure was reached by 7 am. Their work was the toughest because of the heat and the carbon dioxide, which made the air unbreathable.
The machinists who arrived around 6:0 were in charge of preparing the machine and ensuring its proper functioning for the whole day. The oilers were in charge of constantly filling the 48 "drip" grease fittings and used burettes to lubricate 315 oiling points every half-hour. The men worked to the rhythm of the foreman's whistle, the only way he could be heard above the noise of the alternator.
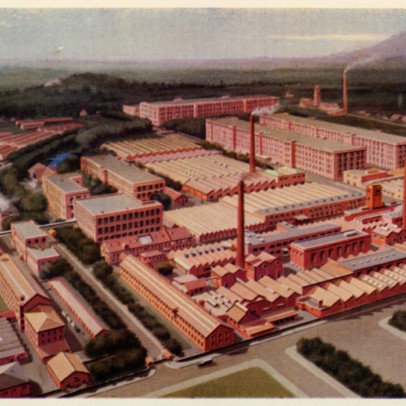
A thoroughly restored heritage
Transferring the "Great machine" from the DMC plant to the brand new museum building required complex logistics and the expertise of specialists. The machine had to be completely disassembled, part by part, then restored before being put together again. The objective was to have it in running condition for the visitors of the museum.
Great care was brought to the materials used for the restoring project. It was necessary to renovate or reproduce certain parts that had been too badly damaged. After over 20,000 hours of work the wheel turned once again on 18 November 1985, more than two years after the start of the process. The machine was started up using steam produced by an electric boiler.
Today, two electric motors drive the rotor. In order to function properly it still requires application of lubricants every hour to the 315 oiling points and the grease fittings. The rotation speed of the wheel is 21 turns per minute, which is four times less than in 1901...