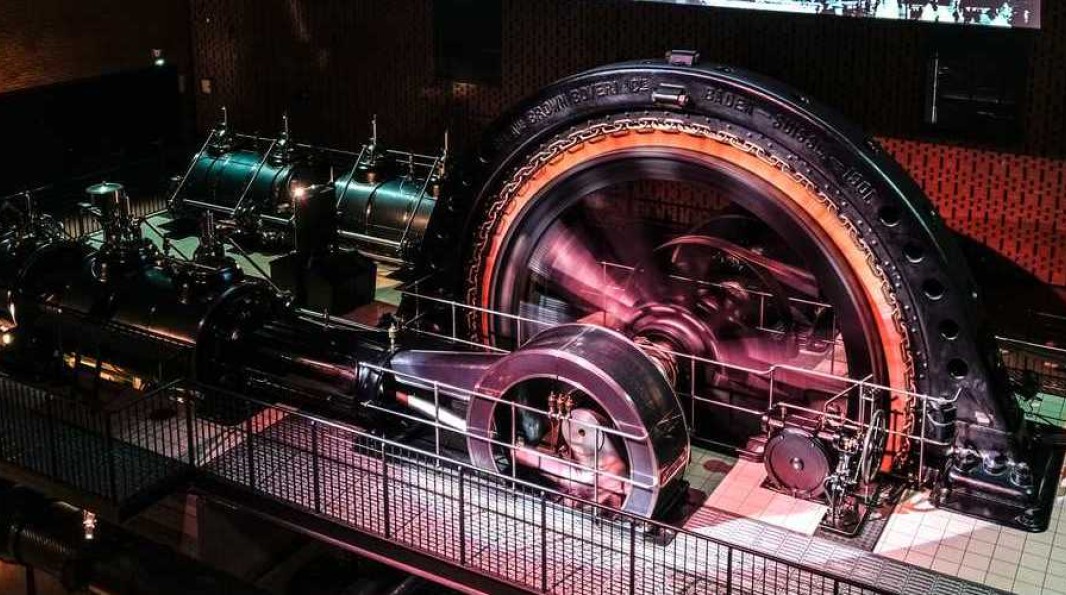
Pièce maîtresse de la collection, la grande machine Sulzer-BBC à l'origine de la création du musée, a alimenté en électricité la filature D.M.C. (Dollfus Mieg et Cie) à Mulhouse, de 1901 à 1953.
Sauvée de la destruction au tournant des années 1980 grâce à la volonté de quelques industriels et passionnés d'histoire, elle est alors restaurée et transférée dans le bâtiment principal du musée, créé à cette occasion. Celle que l'on nomme communément « la Grande Machine » est aujourd'hui l'un des fleurons du patrimoine industriel mulhousien.
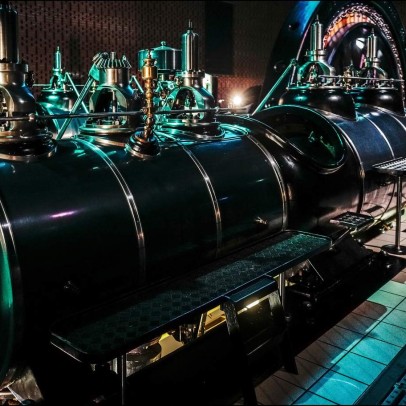
Un monstre de métal de 170 tonnes
Le groupe électrogène de fabrication étrangère est composé d'un alternateur Brown-Boveri et Cie (BBC) fabriqué en Allemagne à Mannheim- actionné par une machine à vapeur Sulzer, réalisée à Winthertur (Suisse).
Il illustre parfaitement la transition technologique entre l'utilisation de la vapeur, principale énergie utilisée lors de la première industrialisation, et l'électricité devenue l'énergie de la seconde industrialisation.
Les chaudières produisaient alors de la vapeur d'eau à une pression de 12 bars afin d'actionner les quatre pistons de la machine à vapeur contenus dans les quatre cylindres haute pression, moyenne pression, et basse pression pour deux d'entre eux. Le mouvement des pistons fait tourner la grande roue de l'alternateur par l'intermédiaire des bielles et de manivelles. La roue joue aussi le rôle de volant d'inertie : sa masse régularise le mouvement de la machine.
Elle produisait jadis du courant alternatif grâce aux 72 électroaimants qui la composent et qui étaient alimentés en courant continu par une dynamo appelée excitatrice. Les pôles de ces électroaimants sont alternés : un nord, un sud...
Lorsque la roue qui constitue le rotor de l'alternateur tournait, l'inversion rapide du champ magnétique devant la partie fixe -le stator- générait un courant électrique alternatif dans ses induits en cuivre. L'alternateur produisait alors un courant d'une puissance de 900 KW pour une tension de 400 V et une fréquence de 45, puis 50 Hz à partir de 1922.

Une machine et des hommes
Un personnel qualifié assurait le bon fonctionnement de la machine. Dès 4h30 du matin, les chauffeurs alimentaient la chaudière en charbon permettant d'atteindre vers 7h la pression nécessaire. Leur travail était de loin le plus pénible en raison de la chaleur et de la présence de gaz carbonique qui rendaient l'air irrespirable.
Les machinistes arrivés vers 6h30 avaient pour tâche la préparation de la machine et veillaient à son bon fonctionnement tout au long de la journée. Les graisseurs remplissaient sans relâche les 48 huileurs « goutte à goutte » et effectuaient à la burette le graissage de 315 points, toutes les demi-heures. Le travail des ouvriers était rythmé par les coups de sifflet du contremaître, seul moyen de se faire entendre en raison du bruit de l'alternateur.
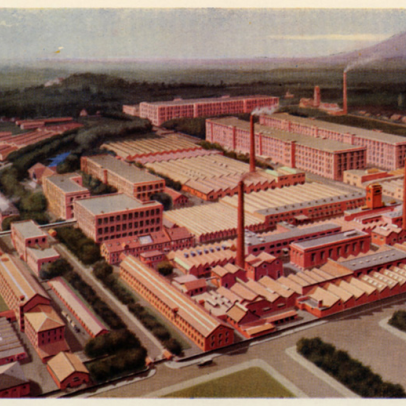
Un patrimoine entièrement restauré
Le transfert de « la grande machine » de l'usine DMC vers le tout nouveau bâtiment du musée a nécessité une logistique complexe et les compétences de spécialistes. Il a fallu pour cela démonter cette impressionnante mécanique pièce par pièce, la restaurer avant de la remonter, l'objectif étant de la faire fonctionner pour les visiteurs du musée.
La restauration s'est faite dans le respect des matériaux. Il s'est également avéré indispensable de reconstituer ou de reproduire des pièces trop endommagées. Après 20 000 heures de travail, le premier tour de roue a lieu le 18 novembre 1985, soit plus de deux ans après le début de l'opération. Cette remise en marche s'est effectuée en utilisant toujours la vapeur produite au moyen d'une chaudière électrique.
Aujourd'hui ce sont deux moteurs électriques qui entraînent le rotor. Son bon fonctionnement requiert toujours l'entretien toutes les heures, des 315 points de graissage et des huileurs. La vitesse de rotation de la roue est de 21 tours par minute, soit quatre fois moins qu'en 1901...